With the rapid development of robotics, the Integrated Robotic Joint Module (IRJM) has become a critical component in robotics, attracting widespread attention from both academia and industry. This article explores the basic principles, design characteristics, technological advantages, application prospects, and challenges of the integrated joint module. It also analyzes the importance of this technology in future robotic applications, based on academic research and the practical needs of the industry. This report proposes potential technical directions for the development of this field and offers an outlook on future applications.
1. Introduction
In robotics, the joint system is one of the key components that determines the robot’s precision, flexibility, and load-bearing capacity. Traditional robotic joint designs typically consist of multiple separate modules, which results in high design complexity and poor system coordination. However, with the introduction of the integrated design concept, the Integrated Robotic Joint Module (IRJM) has emerged as a new-generation robotic joint technology, combining the drive system, sensors, control modules, and mechanical structure into a compact unit. This has successfully addressed some of the shortcomings of traditional designs and has found applications in several fields.
With the rapid advancement of automation technology, artificial intelligence, and robotics, robots are becoming increasingly integrated and intelligent. The IRJM exactly meets these needs by reducing the connection and interface issues inherent in traditional multi-module designs, enhancing overall system performance, and enabling robots to better meet the demands of high-speed, high-precision, and complex tasks.
2. Definition and Components of Integrated Robotic Joint Module
2.1 Definition
The Integrated Robotic Joint Module (IRJM) refers to a component that integrates several functional modules (such as motors, drive systems, sensors, and control systems) into a single unit to perform the functions traditionally completed by multiple parts. Compared to traditional separate designs, this approach is more streamlined and efficient, while also reducing system failure rates and improving overall robot performance.
The IRJM not only features a compact size but also boasts superior coordination and reliability, enabling robots to execute a variety of complex tasks with higher accuracy. This design is especially critical in high-performance applications such as industrial automation and medical robotics.
2.2 Key Components
The IRJM typically includes the following key components:
- Drive System: Including motors and transmission devices, it provides the motion power for the robot’s joints. Typically, stepper motors, servo motors, etc., are used to ensure precise control and stable output during the movement process.
- Sensors: Used to monitor joint angle, speed, load, and other parameters, and provide real-time feedback to the control system to correct and adjust the robot’s movements.
- Control Module: Responsible for receiving sensor data, processing signals, and controlling the drive system to execute precise movements. The control module usually utilizes embedded microprocessors and supports various communication protocols.
- Mechanical Structure: The outer framework of the joint, which supports and connects the various components while bearing the load during movement. This component needs to meet mechanical requirements to ensure stability and reliability under load.
3. Technological Advantages and Challenges
3.1 Advantages
- Integrated Design: By integrating multiple components into a single unit, the IRJM reduces the number of components in the system, simplifying design and manufacturing, while improving system reliability and stability. This also reduces failure rates by eliminating connections and interfaces between multiple parts.
- Increased Flexibility and Precision: Since the control and drive systems are consolidated into one module, the feedback time is significantly shortened, enabling robots to maintain high flexibility and precision during complex tasks. For example, in precision manufacturing or minimally invasive surgery, the high-performance control system of the IRJM ensures the precise adjustment of joint positions and speeds, guaranteeing accurate task execution.
- Efficient Drive and Miniaturization: The IRJM adopts efficient drive systems while maintaining a compact design, suitable for applications with stringent size and weight requirements, such as micro robots and medical robots. This allows robots to perform tasks in smaller spaces, particularly in medical procedures and cleaning robots.
- Lower Failure Rates: Integrated designs reduce interfaces and connections between multiple components, leading to lower failure rates compared to traditional robotic joint modules. This enhances overall system reliability, making robots capable of continuous operations in industrial and medical settings.
3.2 Challenges
- Manufacturing Cost: The production of IRJMs involves the integration of several high-precision components, often leading to higher manufacturing costs, especially in high-load and high-precision applications. The use of advanced manufacturing technologies and specialized materials can significantly increase production costs.
- Technical Complexity: Integrating multiple functions into one module requires high technical expertise in areas like motors, sensors, and control systems. This presents challenges in product development and technical implementation. Balancing the efficiency and coordination of these components remains one of the technical difficulties.
- Load and Efficiency: In high-load applications, the IRJM must balance power output and efficiency to avoid overheating or system failure. Improving energy efficiency and reducing energy consumption will be key areas for future development.
- Environmental Adaptability: Although the IRJM excels in precision and flexibility, its durability and reliability may face challenges in extreme environments (e.g., high temperatures, humidity, or harsh weather conditions). Therefore, environmental considerations need to be incorporated into the design to ensure stable operation under diverse conditions.
4. Application Fields
4.1 Industrial Automation
The industrial automation sector demands high precision and stability in robotic joints, particularly in repetitive tasks such as assembly, welding, and material handling. As Industry 4.0 advances, the demand for robots in manufacturing is increasing, especially in complex factory environments where robots need to perform precise tasks. The IRJM stands out in these applications due to its ability to operate with high precision and stability, improving production efficiency.
4.2 Medical Robots
Medical robots are gradually being adopted in operating rooms and rehabilitation fields, where precision and flexibility are crucial. By adopting IRJMs, medical robots can achieve accurate surgical operations, particularly in minimally invasive procedures. For example, robotic systems like the da Vinci Surgical System leverage IRJMs to precisely control surgical instruments, reducing risks and trauma during surgery, thus enhancing treatment outcomes.
4.3 Service Robots
As demand for smart homes and personalized services increases, service robots such as cleaning robots and security robots are becoming more widespread. For these robots, the IRJM enhances mobility and reduces system complexity, providing an efficient and cost-effective solution for the consumer market. For instance, robotic vacuum cleaners use integrated joint modules to achieve efficient movement and cleaning, while minimizing system failures.
4.4 Consumer Electronics and Entertainment
In the consumer electronics and entertainment sectors, robotics applications are expanding beyond single-purpose functions to more multifunctional and intelligent applications. Smart toys, educational robots, and other products use IRJMs to execute complex movements, improving user experience and attracting more consumers. For example, modern interactive toys mimic human movements, engaging with users in more realistic ways.
5. Future Development Directions for IRJMs
5.1 Intelligent and Adaptive Control
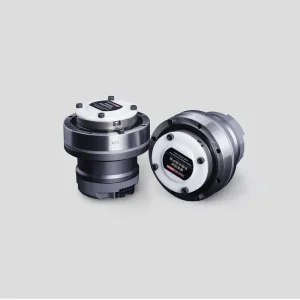
With the rapid development of AI, machine learning, and other technologies, future robots will be more intelligent, capable of adapting to changing environments and tasks. The IRJM will integrate with these intelligent control technologies to give robots stronger autonomous decision-making and adaptability. Future joint modules might even possess self-healing capabilities, adjusting automatically in case of faults to ensure stable operation in complex environments.
5.2 Higher Integration and Miniaturization
With advancements in nanotechnology and miniaturization, future IRJMs will become more compact and lightweight, suitable for applications in even more confined spaces, such as micro medical devices and exploration robots. Miniaturization technology will help robots perform tasks in more limited spaces while reducing energy consumption and improving efficiency.
5.3 High Efficiency and Low Energy Consumption
To meet environmental sustainability demands, future IRJMs will need to achieve higher energy efficiency. As battery technology progresses, low energy consumption and long battery life will be crucial for the design of future joint modules. Additionally, the application of energy recovery systems could further improve the efficiency of IRJMs, reducing energy waste.
6. Conclusion
As an essential component in robotic technology, the IRJM offers a range of advantages, including integrated design, enhanced flexibility, and precision. Despite current challenges related to technical implementation and manufacturing costs, the IRJM is poised to play an increasingly important role in the development of robotics. The analysis presented in this report aims to provide insights for researchers and engineers in related fields, contributing to the continued advancement of integrated robotic joint module technology.